CNC Machining: Revolutionizing Manufacturing with Precision and Effectivity
CNC cutting and milling has transformed manufacturing by providing the most precise and effective method for producing parts and components across an array of different industries. This cutting-edge technology utilizes computer-controlled machinery to perform cutting or drilling, milling and other operations on various kinds of materials like metals plastics, and wood. The level of precision achieved by CNC machining is unparalleled which allows complex plans to be made in a highly precise manner. With the replacement of manual work with automated processes, CNC machines have significantly reduced the possibility of human error and increased production speed. The combination of precision with efficiency has made CNC machines an essential element of manufacturing today.
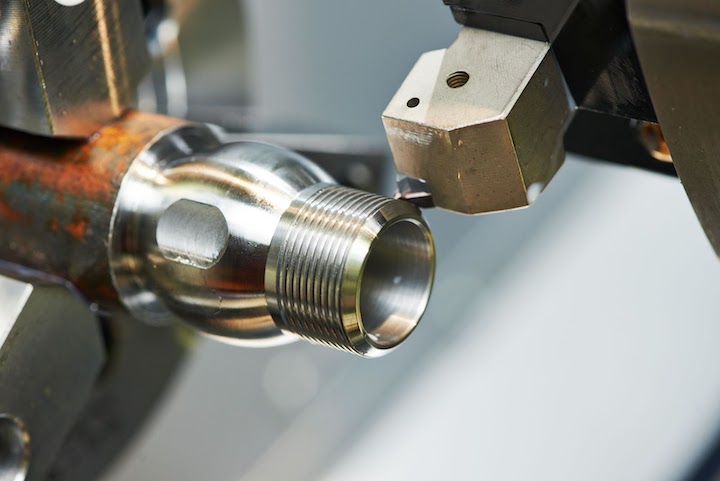
The primary advantage of CNC machining is its unparalleled precision, and the ability to make intricate designs. In contrast to manual machining, in which the operator controls an instrument, CNC machines follow programmed instructions to cut, shape, and sculpt materials with tremendous accuracy. It reduces the possibility of error significantly, allowing for production of components which are precisely designed. The most intricate geometries and parts, and precision tolerances are all possible with CNC machining, making it ideal for industries that require high standards of accuracy. This includes aerospace, where even tiny deviations in parts can have serious effects.
The effectiveness of CNC processing is yet another major factor in its widespread adoption. Traditional methods for machining call for highly skilled workers to operate the machinery, adjust settings, and change tools for each operation. This process is not only labor-intensive, but it is also susceptible to human error. CNC machining on the contrary, can automate these jobs, enabling machines to run continuously with the least amount of supervision. Once the program is set and the machine is loaded with the required material and equipment, it is able to perform several actions without interruption, significantly decreasing the time to produce. CNC machines can also be capable working 24/7, making them perfect for big production runs. This level of efficiency enables manufacturers to meet the tightest deadlines, enhance their output while reducing labor costs as well as maintain high-quality standards.
The CNC parts brand also has excellent reproducibility, assuring that each piece produced is identical to the design originally. This is essential when industries require the massive production of components that are standard including automotive parts and consumer electronic components. Because CNC machines follow programmed instructions, they can produce hundreds, or even thousands of parts with very few variations in their quality. This ensures the reliability of the final products, but it also minimizes loss, since fewer pieces get rejected because of defects. In addition, as the design software used in CNC machine machining are easily altered or upgraded, companies can quickly adapt to changing specifications for their products or the demands of their customers, without the expense of refalibration or retooling.
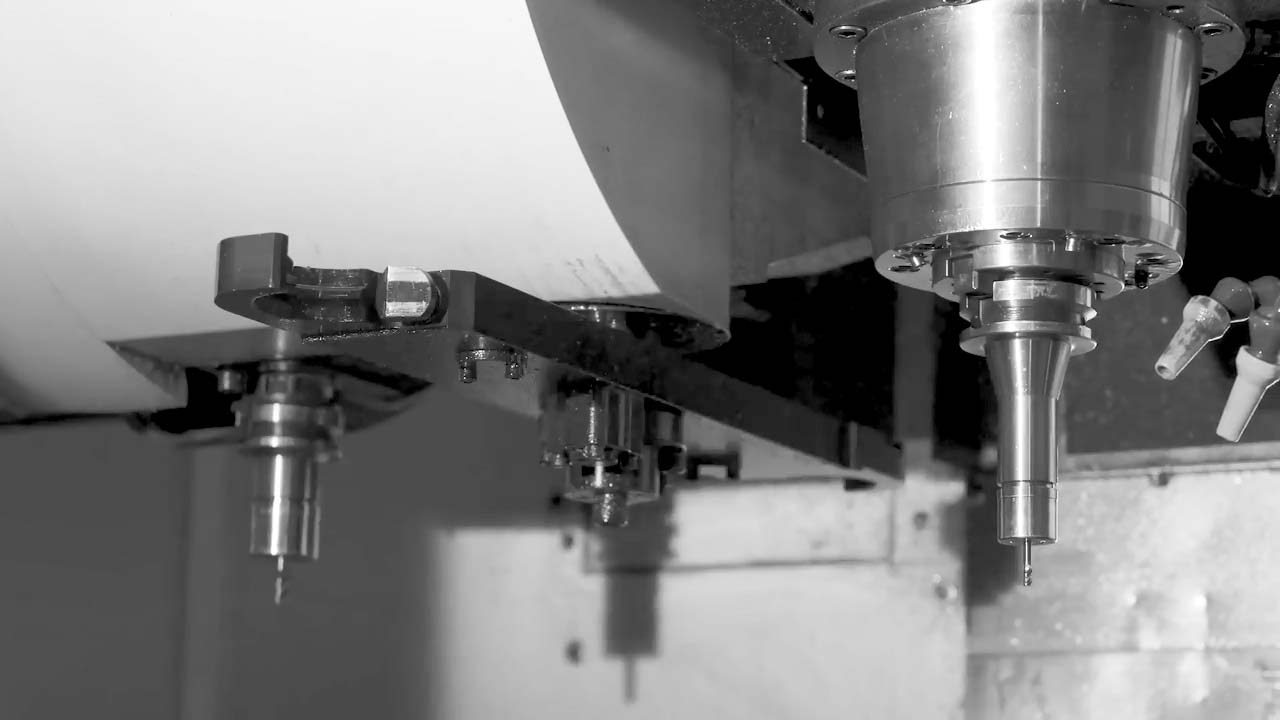
Despite its many advantages, CNC machined work is not free of the challenges. One of the main obstacles to many companies, especially small - and medium-sized companies in the beginning is the investment necessary. CNC machines cost more than conventional machining equipment, plus there's an expense for specialized software maintenance, operator instruction to think about. But the benefits over time, such as reduced labor costs, faster production cycles, and increased quality of parts - often justify the initial cost. Also, the rise of CNC machine service providers permits those who do not have capital to buy their own machines to still take advantage of the technology. These companies can make custom parts on demand providing a low-cost solution to businesses who require precision cutting without incurring upfront expenses.
Future of CNC machining is bright, the advancements in technology are constantly expanding the limits of what machines can accomplish. As CNC machines get increasingly sophisticated, they're increasingly integrated with other technologies including 3D printing and robotics, creating hybrid manufacturing methods which combine the advantages of multiple techniques. In addition, the growth of smart manufacturing and technological advancements like Industrial Internet of Things (IIoT) has led to greater connectivity and automation in CNC machining, allowing the machines to interact with each other and adjust operations with real-time the data from sensors. While these advancements continue to develop, CNC machining will remain essential to the advancement of manufacturing technology that will offer even higher precision along with speed and adaptability for the coming generations of goods.